We’ve been experiencing main line clogs periodically for years. I’ve assumed the big pipe in the front yard was to blame. Once every 18 months give or take we would have to have it rooted. I considered proactively replacing the iron pipe in the front yard but the best quote was about $6500 and would have to tear up part of the driveway adding a few thousand more to that. At that rate and cost it was easy to kick the can down the road, especially since a couple cameras down the line showed nothing but a rusty iron pipe.
Then it rapidly got worse. Once a year instead of 18 months, then three times in less than a year. That third time a camera was run down the line and a break was identified under the kitchen floor. I decided that it was time. The plumber identified the spot, “it might be under that cabinet but as best I can tell it is here”. So on day one a different team from the company tore into the slab and determined it was under the cabinet. Then I had to remove the cabinet before they could come back. The cabinets were all interconnected but I managed a fairly clean cut from the rest of it and removed the section that was in the way.
They came back and tore up more slab. Found that leak and fixed it but found another leak by the sink and then another leak on the opposite side where two lines converged. I then had to tear out the rest of the base cabinets from one side of the kitchen to the other. All of them. At this point, I had learned that every line in the house save the downstairs half bath met in the kitchen and would be impacted.
On the third day they repaired the leak under the sink and there was concern that the remaining leak would be just inside the living room (and technically it might have been) but they were able to tunnel into the hole and repair it. The problem was that these PVC pipes in the slab had disintegrated after nearly 50 years and the bottom half was gone. Just gone, like a straw cut lengthways. So every drop of water that flowed through there picked up some dirt and moved it to deposit it somewhere else.
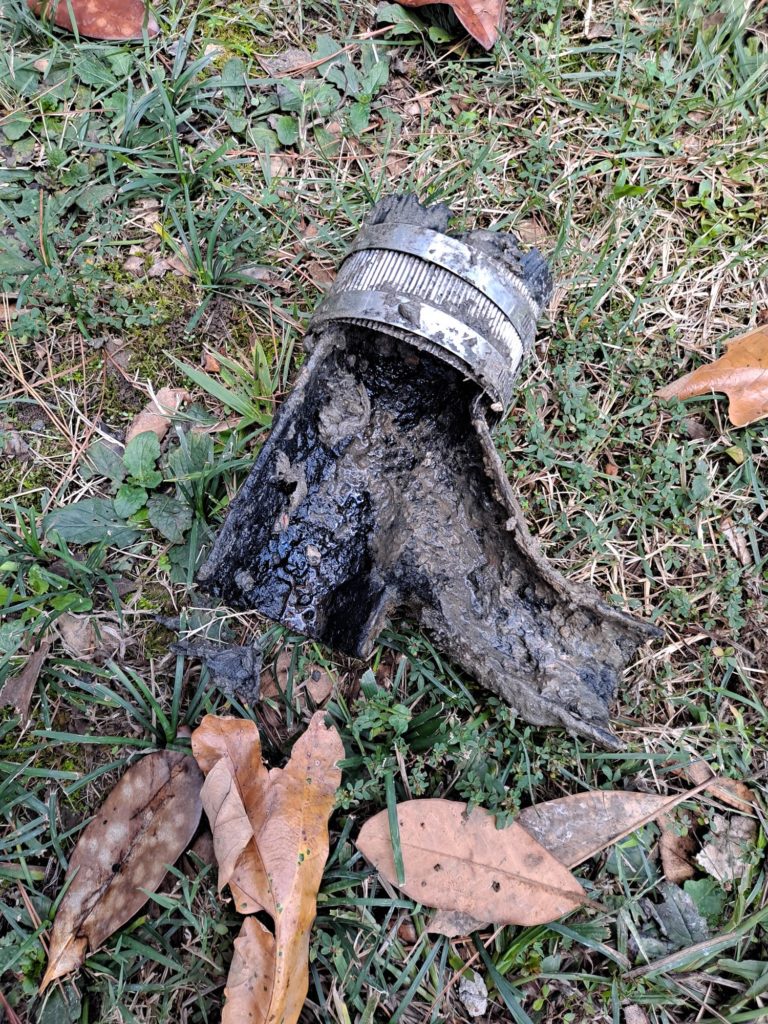
So finally, after three days of jack hammering spread over eight days, the leaks were repaired. The plumber ran the camera as far as it would go (which was to under the driveway) and could find no other issues. I paid them and then started the recovery.
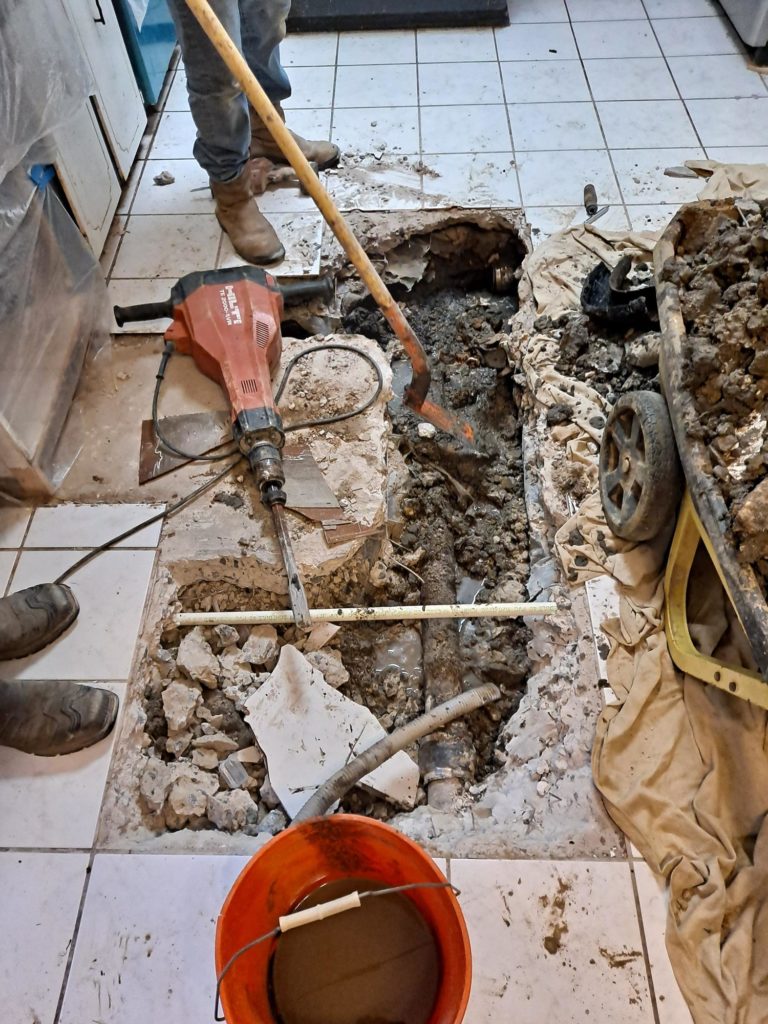


That was a Wednesday, in the middle of October. I received an initial check from the insurance company the next day so I had some money to start the recovery with.
First order of business was to repair the slab. On Saturday, I rented a concrete mixer and used ten or so bags of Quickcrete and six bags of leveler to repair the slab. Since they had by necessity destroyed tiles (which could not be matched after fifty years) I also put down some plywood underlayment to level the floor before putting down vinyl planks.
I took scrap plywood from the old cabinets and built a temporary sink stand and a two-shelf table to hold stuff so that we could live while this was all going on.
The following weekend, I put down flooring covering about 75% of the kitchen and then finished it the next Saturday. I’m not very good at this but the insurance, which I was very grateful for, was enough for materials not enough to pay someone to do it. That said, I did reach out to someone about putting down the floor but never heard back. That’s another thing, who wants to wait two months for a professional to be able to come?
While all of this was happening, I ordered new base cabinets. I found that cabinets that had to be shipped to the store were significantly cheaper than the identical (except for part number) items in the store so I went the cheaper slower route. It’s not like I had a place to keep them anyway.
While wandering Lowe’s, I came across some Pine-Spruce glued boards that were very pretty and came in widths of as much as 24″ nominal and lengths from 36″ to 96″ actual. These would make excellent countertops. More research found six of these with an actual thickness of 1″ instead of 1″ nominal at another Lowe’s and I nabbed them while they were still there. This gave me enough board to do the cabinets with one mistake. I mean, I was allowed to make one mistake and still have enough.
So, by this time it was early November and the floor was down. I had my first pair of cabinets which would be secured together to make one unit next to the refrigerator. I painted them and got them ready to use if not finished. A few days later the first countertop had been stained and coated with polyurethane and put on it’s top.
Since the 40 year old range was built into the old cabinets and since it was 40 years old, I splurged and got a new 21st century model. It does a lot more than I know how to do so far. I felt a little bad because that old stove just kept working but I reminded myself that it was not sentient and was not aware that I gave it to someone for parts.
The cabinets trickled in over the next couple weeks. By Thanksgiving they were all in place though the countertops were not fully finished. Since I had made my one allowed mistake, I could not afford to make another, so I took my time and did not prepare the countertops before I had the cabinets ready. Better that than a trip to Branson for the closest similar board. Unlike the previous cabinets, these are modular and can be taken apart with wrenches and screwdrivers rather than hammers, saws, and crowbars.
At this writing, the big stuff is done but there is plenty of little stuff left to do.
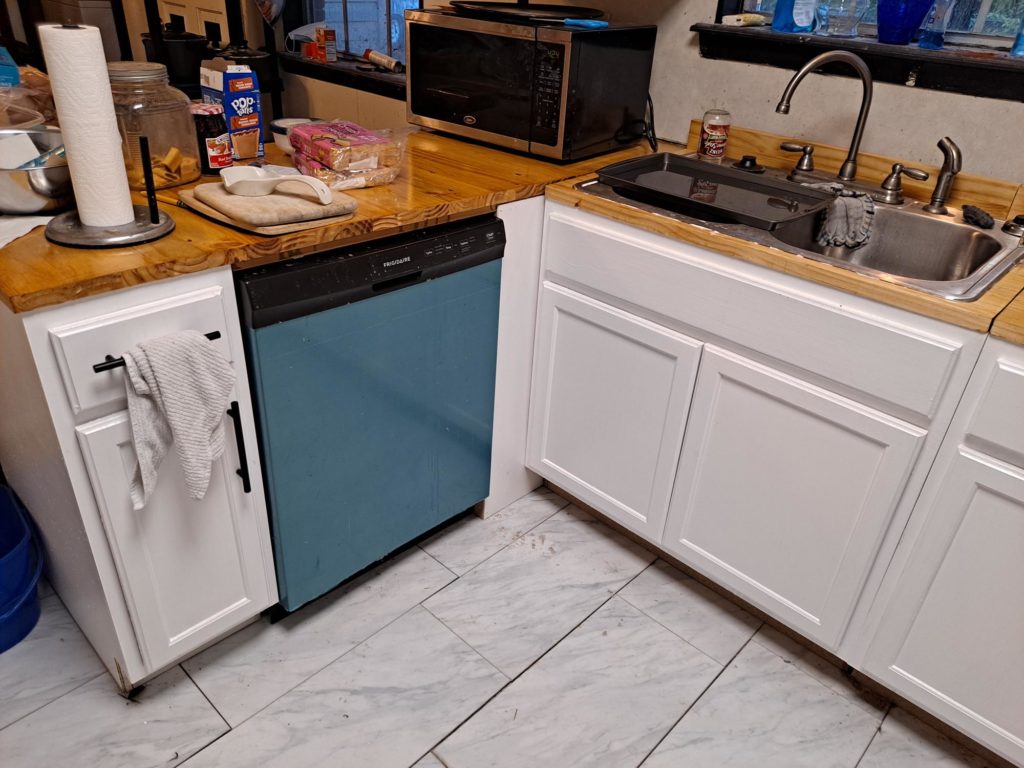
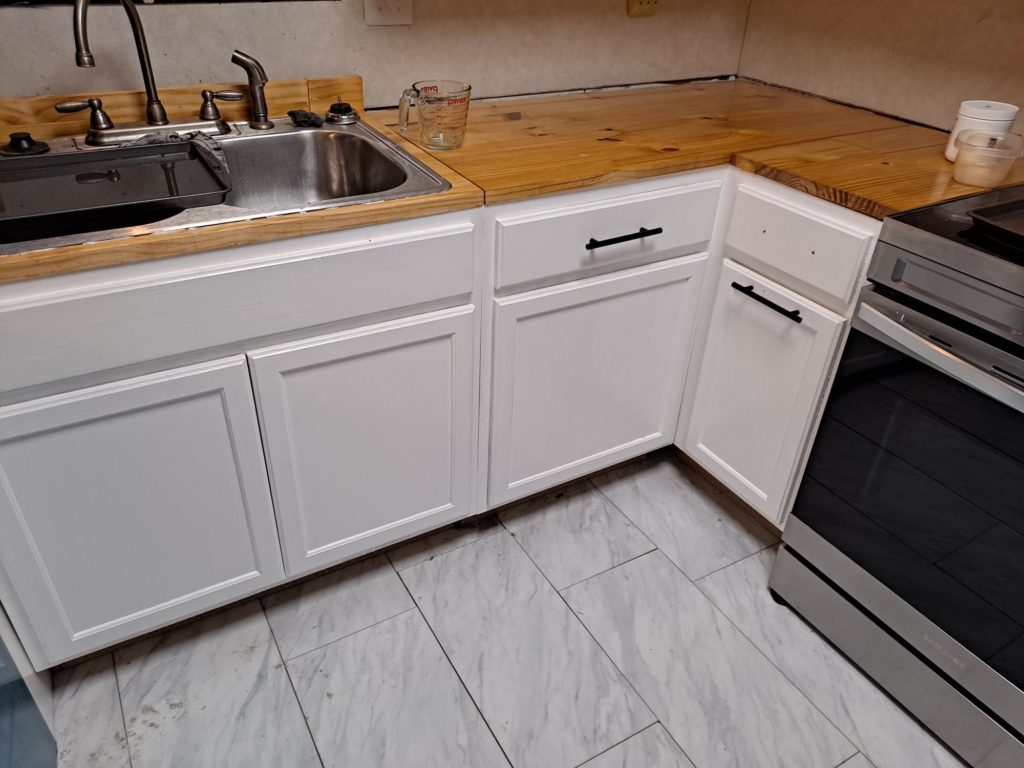
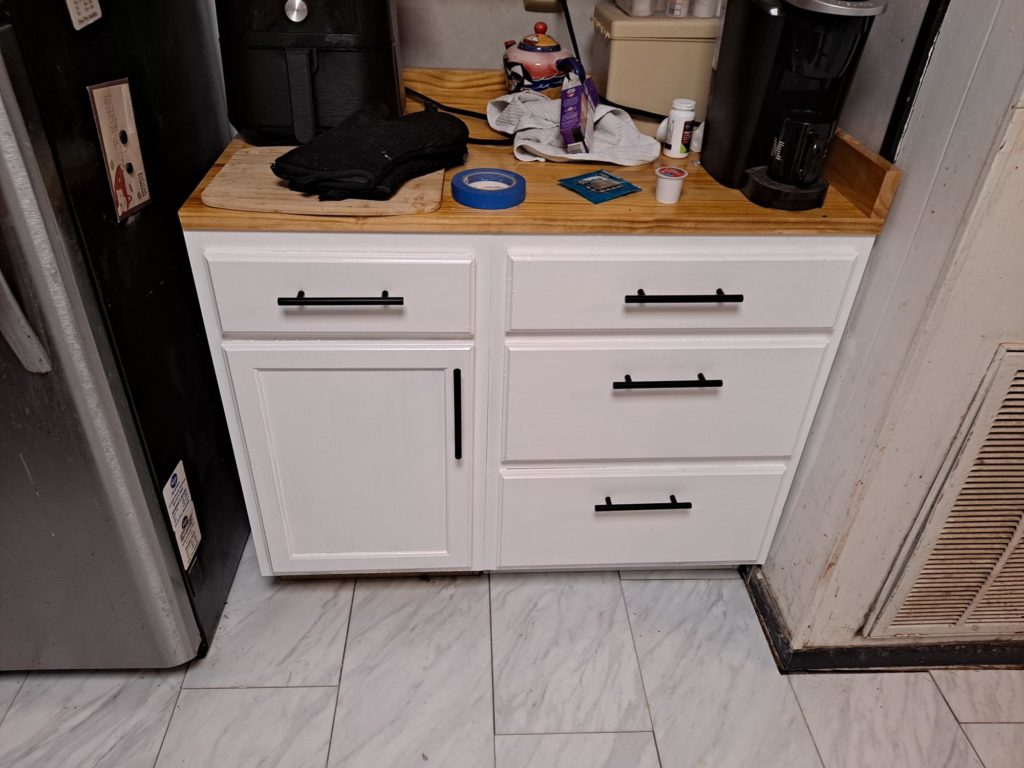